Polypropylene Fill For Cooling Towers And Other Applications
For cooling towers and other applications, (waste water treatment, fish farms for example). 2H Plastics (Australia) has introduced to the Australian market a new fill. This fill is made in high quality Polypropylene, instead of the commonly used PVC.
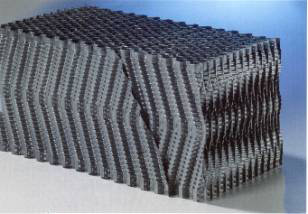
The PP sheets are welded together to form a strong block. The welding is much stronger and longer lasting compared to the only glued PVC blocks.
The Polypropylene (PP) foils are extruded (incl. embossing) directly from the molten mass. Thanks to this patented process the customer receives a number of benefits:
Advantages of extruded and welded polypropylene packing
Optimized foil thickness distribution:

Foils are reinforced both at the outer edges as well as in the middle by approx. 50%, i.e. at places that have been defined beforehand, the foil is extruded thicker than at other places. Thanks to this optimized foil thickness distribution, we achieve a unique stability at the top and bottom edge of the block (both at a block height of 300 mm and 600 mm). With that, an extraordinarily high resistance is achieved against the danger of erosion (pitting) caused by the constant admission of water. Our PP packing that consist of a PP compound developed by us, have a particularly high strength and erosion resistance.
Deformation behavior (memory effect)
During conventional methods for the manufacture of embossed foils for packing, a flat foil that has been prior extruded is subsequently heated and then formed (e.g. by deep-drawing). The severe deformation during this process causes stresses inside the foil. These stresses become obvious during renewed heating when the foil shows a tendency to return to the shape of a flat foil. This is called the memory effect. During malfunctions in the cooling tower operation or even during storage when exposed to sunlight (e.g. during the installation phase), temperatures may occur that can trigger this memory effect and cause a deformation of the packing and therefore also a reduction of the refrigerating capacity. These problems are unknown with the 2H-production method, as our foils are formed directly from the molten mass so that they are absolutely free of any stresses. The customer will, therefore, receive a product that will retain its shape both during the installation phase and during its operating life.
Temperature resistance
Download PDF Brochure Below:

Malfunctions in the cooling circuit may lead to hot water exceeding maximum design temperature coming in contact with the packing. Furthermore, there are numerous applications during which higher than normal water temperatures may occur. In their standard design, our PP-packing resist operating temperatures of up to 80°C (short-term) without any deformations. At operating temperatures exceeding 80°C (long-term), it is possible for us to use a PP-compound that has been specifically adapted for this purpose so that even under these extreme conditions (short-term up to 120°C), our packing can be used without any problems. PVC-packing is restricted in their temperature resistance and their operating temperature should not exceed 60°C (short-term). At a permanent water temperature of 60°C or more, there is a danger that extreme deformation of the packing will occur.
Bonding technique
The welding method that has been specifically developed by 2H makes it possible to completely dispense with the use of glue. By our method, the foils are heat fused together. Depending on the type of packing, up to 20,000 welding spots per m2 guarantee an excellent bonding of the foils absolutely without any solvents! This is not only beneficial to environmental protection, but eliminating glue also avoids the creation of any points susceptible to hydrolysis, which could cause the contact points to fail.
The superior strength of our bonding method (load-bearing capacity up to 30,000 kg/m2) has been confirmed in long-term tests carried out by accredited testing laboratories (inter alia TÜV, the German Technical Inspection Agency).
Summary:
Advantages of the 2H-packings made of polypropylene (with 2H PP-compound)
Today, polypropylene is the material most frequently used as a substitute for PVC. Specifically, when used for fill in cooling towers, it offers several advantages over PVC, namely:
- an improved temperature resistance (standard design short-term up to 80°C, special design long-term up to 100°C) offers safety during malfunctions and allows a wide range of applications
- a low tendency to embrittlement and thus substantially more resistance to erosion (no pitting)
- small danger of damage to the packing during the installation phase due to the raw material properties of PP (tough material)
- excellent UV-stability
- thanks to the lower density of PP compared to PVC, it is possible to achieve a higher wall thickness at equal weight per m? which results in a super proportional increase in the stability of the packing
- in many applications, it is more resistant to chemicals than PVC
- PP is free of halogen and heavy metals, and thus less ecologically harmful
- 2H PP-products have been approved for drinking water applications
- simple, trouble-free disposal (see publication of EU-Commission; download: http://europe.eu.int/comm/environment/pvc/contributions/3greenpeace.pdf)
2H polypropylene (PP) packing offer a high-quality alternative to the PVC packing currently available on the market at a very competitive price. The customer receives a product that, after years of use will, still display the same excellent properties as when it was new.
Download PDF Brochure Below:
